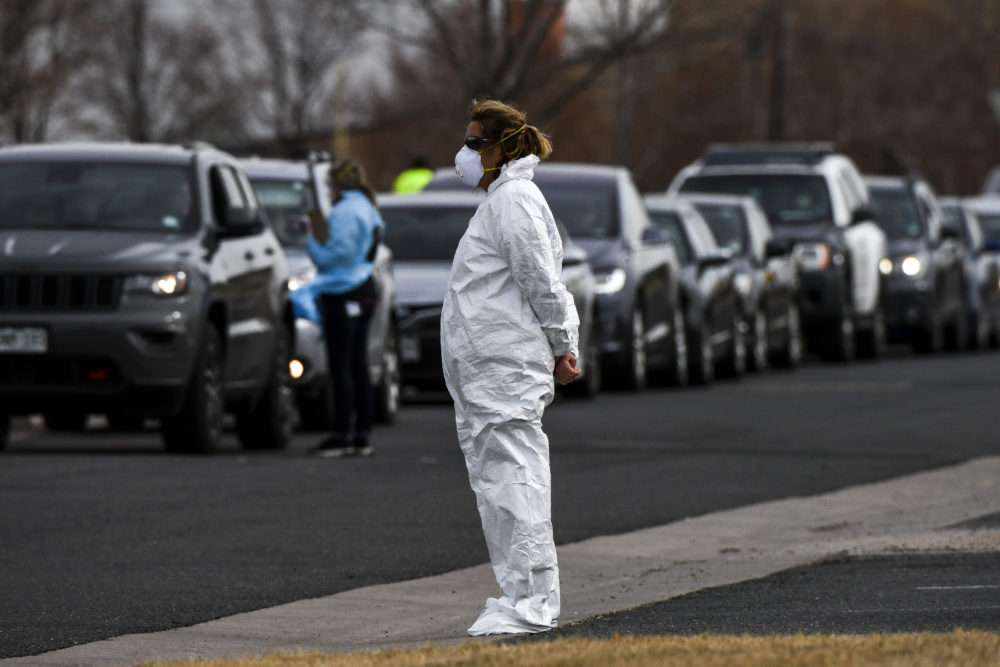
Due to the spread of the novel coronavirus, hospitals are reaching or exceeding capacity and medical personnel are seeing more patients than ever before. As a result, healthcare facilities are running out of critical personal protective equipment (PPE), such as face masks and shields. Medical workers are forced to reuse items originally designed for single use, which is unsafe for both workers and patients. Although the Centers for Disease Control and Prevention (CDC) reports that in Colorado, car accidents are the third most common cause of death, some experts believe that COVID-19 could soon become one of the most common causes of death throughout the country.
A number of companies are now using three-dimensional (3D) printing to produce needed medical gear. 3D printing is a manufacturing technique that produces objects by applying layers of materials such as metal and plastic. Some 3D printers resemble the kind of inkjet printers commonly found in offices and homes — but instead of producing printed sheets of paper, they create 3D objects using a computer-aided design (CAD) file.
3D printing is poised to revolutionize medicine, especially since it can create living human tissue. About 20% of people in the United States do not have an ideal bite, which is probably why about 4 million Americans are currently wearing braces. Some patients have created their own braces using 3D printing, while medical personnel frequently use this process to make prosthetic limbs and rebuild tissues.
On April 3, the Food and Drug Administration (FDA) gave its approval for the first mask produced through 3D printing to be used as protective gear by medical personnel treating COVID-19 patients. The Stopgap mask was created by a team from the Veterans Health Administration (VHA) Innovation Ecosystem. It fits securely around the nose and mouth and is held in place by straps around the ears. It can be easily disinfected and has a filter that can be thrown away and replaced so that the mask can be used again. However, the mask is not intended to replace PPE such as N95 and other masks traditionally used as respirator masks or to be used in clinical settings where airborne exposure to the coronavirus is high.
The FDA has partnered with the National Institutes of Health (NIH) and VHA to speed up the manufacturing of PPE and other medical equipment by 3D printing. They are collaborating with 3D printing company America Makes to speed up approvals for medical gear to be used by personnel treating COVID patients. NIH’s 3D Print Exchange lets anyone with a prototype for a piece of medical equipment to submit it for testing and evaluation by the VHA Innovation Ecosystem.
Now, 3D printing professionals all over the country are banding together to produce face masks, which cover the mouth and nose, and face shields, which protect the entire face with a curved sheet of clear plastic. The University of Southern California (USC) has joined forces with the Southern California Institute of Architecture, UCLA Extension, and other institutions of higher learning, plus over 35 architecture firms and some nonprofit organizations. They are making masks and shields for USC’s Keck Hospital, which will share the gear with other facilities in need.
Companies are also joining the effort to supply medical personnel with PPE using 3D printing. One such company is Stratasys, which originally planned to make 5,000 face shields in the United States at no charge to medical personnel or hospitals. The company is now planning to send out 120,000 shields by April 30. Any business that uses 3D printing and wants to assist Stratasys in producing face shields can complete a form online. Those who want to help can also go to the company’s COVID-19 page and find instructions on printing and assembling face shields. NASCAR, which uses 3D printing to create composite stock car parts, is also producing face shields and making them available to hospitals for free.
Companies using 3D-printing technology are providing other much-needed medical equipment. Formlabs of Somerville, Massachusetts is producing 100,000 nasal swabs every day for COVID-19 testing. SmileDirectClub, a Nashville teledentistry company that uses 3D printing to make dental aligners, also makes a range of medical equipment and is now participating in the effort to make equipment needed in the fight against COVID-19. Automotive companies are also getting involved. Ford is joining forces with GE Healthcare to construct air-pressured ventilators, aiming to produce 50,000 over the next three months. Chevrolet of General Motors has teamed up with Ventec Life Systems to produce ventilators and has promised to make over 50,000 face masks daily. In addition to making face shields, Toyota is working with medical equipment companies to make ventilators at a faster rate.
Even individuals can use 3D printers to make medical gear. The website 3DPrint.com offers extensive instructions for anyone who wants to produce face shields and other equipment at home. And in Detroit, workers at AccelerateKID, a STEM education company, 3D-printed 40 brackets for face shields and brought them to a local hospital. The brackets hold the curved plastic sheet that forms a face shield. AccelerateKID’s two 3D printers can produce two brackets in as little as an hour and a half and can make 10 to 15 brackets daily. American software developer Autodesk is granting free access to its 3D design programs.
Drastic shortages in protective equipment for medical personnel are of great concern. Fortunately, the 3D-printing community is stepping up to meet the challenge of producing these much-needed pieces of equipment on a large scale. Reusing protective equipment that is meant for single use potentially endangers the lives of medical workers and their patients. To work effectively and safely, doctors, nurses, and other front-line medical personnel need an adequate supply of face masks and face shields. And COVID-19 patients with respiratory problems need many more ventilators than are available. Companies and individuals using 3D printers may change all that.