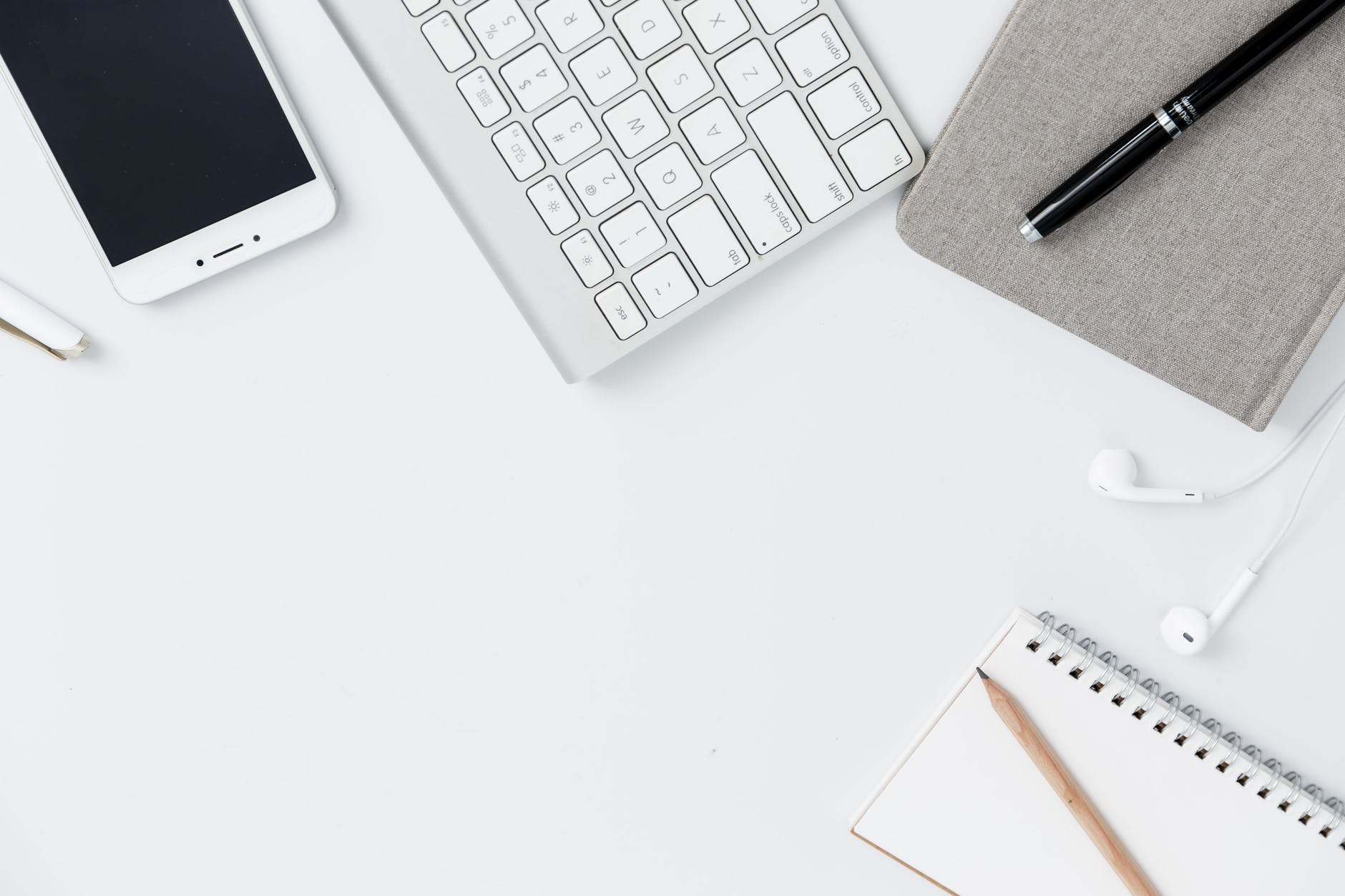
Material Requirements Planning, or MRP, aids in inventory, production, and scheduling by converting a master production schedule into a detailed production schedule that paves the way for timely acquisition of essential raw materials. The control system of MRP is largely based on forecasting to determine the number of raw materials needed to produce, deliver, and meet customer demands. Aside from this, below are some other beneficial things that you need to know about MRP.
MRP Steps and Processes
Generally, MRP is composed of three basic steps, which include identifying the quantity requirements, running the MRP calculations, as well as completing the orders. It is often the case that these processes are executed through an MRP Software that can be a module or a subset of an Enterprise Resource Planning (ERP) system. The calculations run in MRP are largely based on data inputs such as the Bill of Materials (BOM), inventory, and master production schedule. The master production schedule is based on the orders and forecast. From there, the output generated by the system includes the purchase orders, material plan, work orders, as well as reports.
MRP vs. ERP
MRP is more focused on quotes, job costing, sales, orders, controlling stock, purchasing, manufacturing, and invoicing, to name a few. MRP can also be a stand-alone application or a module of ERP. On the other hand, ERP can address all the needs of the business instead of only focusing on the scheduling of resources. For this reason, an ERP system can result in increased efficiency, integrated information, as well as customized reports.
Tips for a Successful MRP
To ensure that your MRP is successful, you need to have reliable and accurate on-hand values. For instance, if you input incorrect quantities in your MRP system, then you can expect that the output that the system will yield will also be inaccurate. Another thing that you need to remember is to use a forecast because your MRP will use this information to produce your requirements. Alongside this, you need to ensure that your data is updated when it comes to your open sales orders, open purchase orders, as well as open production tickets.
Leveraging lead times can also be beneficial because, in doing so, you are providing padding for your quality control team to have ample time in releasing materials to your shipping team. In parallel to lead time, exert the extra effort to perform audits, not only to your vendors but to your shipping performance as well. You will be able to do this by performing frequent reviews of all your historical transactions, comparing your scheduled lead time against the actual lead time recorded.
MRP has several advantages, such as reduced customer lead times, as well as reduced inventory costs. It also paves the way for effective inventory management and optimization, and it improves manufacturing efficiency too. Just keep in mind that, like with any other system, MRP may also have potential drawbacks such as lack of flexibility. Nevertheless, the benefits that you can get from this control system far outweigh the disadvantages you may encounter.